Hot Forging vs Warm Forging vs Cold Forging (Differences & Comparison)
The Differences Between Hot, Warm, and Cold Forging (Advantages & Disadvantages)
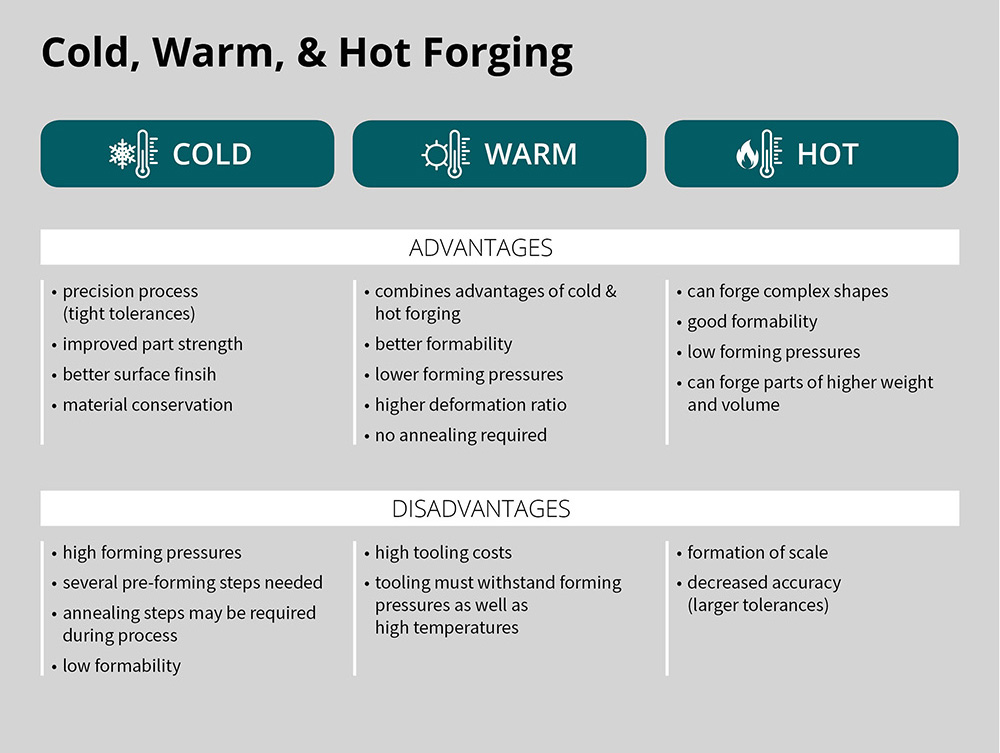
Cold Forging, Warm Forging and Hot Forging
Forging is a process by which a metal object is manufactured into a different shape through localized, compressive forces. Although forging was established as a viable metalworking method thousands of years ago, it continues to be a prevalent craft in the metalworking industry today. In early civilizations, forging was mainly used to create weapons of war, tools, and jewelry, but now there are many types of forging methods available to create metal products for a number of modern-day industries. These industries include agriculture, construction, aerospace, and the automotive industry.
The diversity of the forging market is indicative of the customizable aspect of the forging industry. For example, the forging process can be conducted at various temperatures, depending on the physical properties of the particular materials and equipment involved. Since temperature plays such an important role in the forging process, it is actually used to classify forging methods. These forging methods are known as hot forging, warm forging, and cold forging. They each have advantages and disadvantages, but are chosen based on the intended application of the finished product and cost limits, not simply because one is superior to the other.
What is Cold Forging? (Application & Benefits)
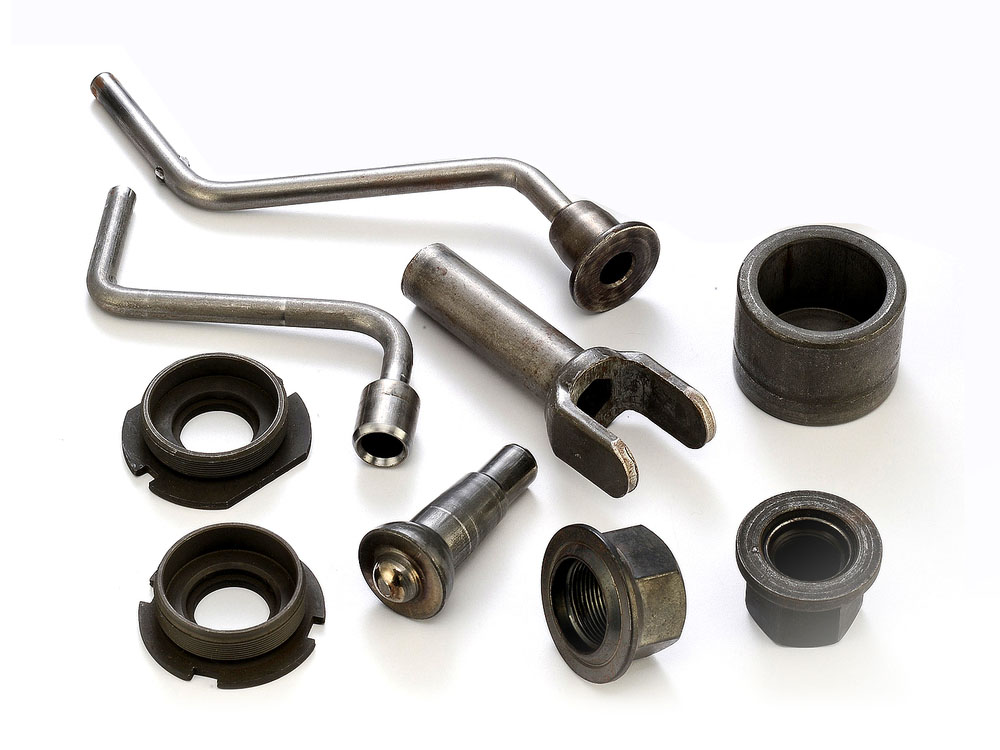
Cold forging takes place at a temperature below the recrystallization temperature of a metal, oftentimes at or near room temperature. Since cold forging is often conducted at much lower temperatures than hot or warm forging, there is a greater resistance to deformation by the workpiece in this process. Therefore, this process typically requires intermediate annealing steps in-between the deformation of the workpiece to minimize strain hardening during the forging process. Annealing is a process that strengthens a workpiece by heating it and then allowing it to slowly cool down in order to remove internal stresses. Since the temperature of the cold forging process is near the hardening temperature of the workpiece, scale formation due to reactions with atmospheric gases is not an issue in this method. On the other hand, the workpiece is not as pliable during the deformation process as with other methods, so greater press loads are needed in order to shape the workpiece.
Cold Forging Temperature Range
Cold forging techniques are known to have the best dimensional accuracy when compared to hotter forging methods. This feature is due to the fact that the workpiece is deformed near the net-shape of the final product. Cold forgings do not have to be cooled down after forging because they are already made near their hardening temperatures. Hot and warm forgings can experience shrinkage as they solidify, a phenomenon that is not an issue in cold forging. Although the workpiece remains in a solid state in cold forging, the strain from friction between the workpiece and the machinery used to deform it can cause the temperature of the workpiece to reach up to 250°C. As a result, the cold forging method is typically used with softer metals such as aluminum, copper alloys, and low alloy steels that usually weigh less than 50 pounds. Softer metals are easier to shape at lower temperatures and require less forging pressures.
Cold Forging Equipment & Material Considerations
A high productivity is associated with cold forging. The working conditions are not only more favorable at room temperature, but are energy-efficient. This environment also yields a high-volume product efficiency. The cold forging process, like the others, improves the mechanical characteristics of the workpiece. The finished product is typically stronger than the starting material. In addition, the dimensions of the final, cold-forged product are the most accurate out of the other forging methods.
The equipment used in cold forging is similar to the other forging methods, but dies must be made of high-resistance materials to reduce wear-and-tear during the forging process. Therefore, engineering design is important in developing suitable equipment for this process. The high costs associated with the equipment are outweighed by a longer operational life.
Advantages | Disadvantages |
|
|
What is Warm Forging? (Application & Benefits)
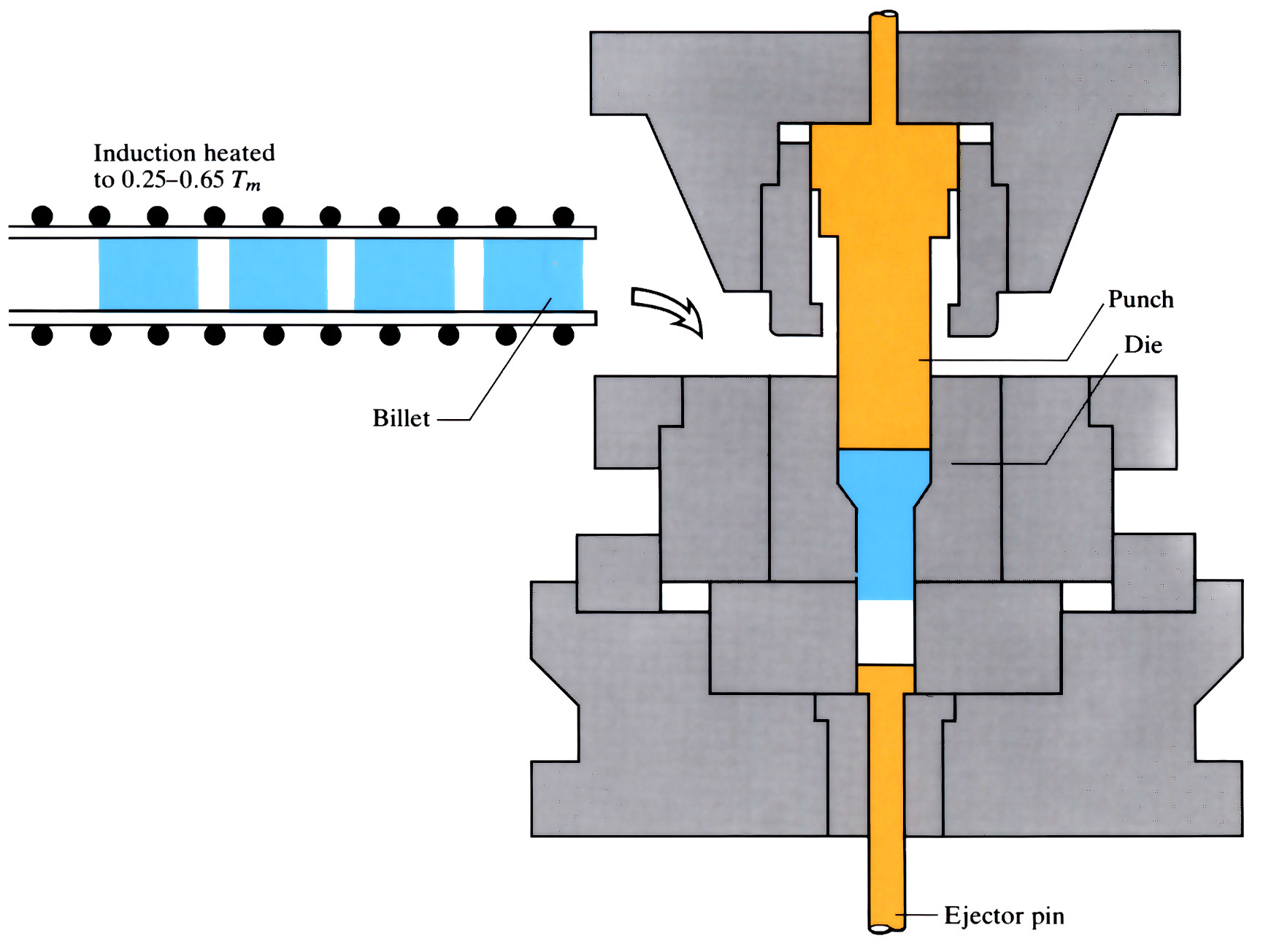
The warm forging process has characteristics similar to both hot forging and cold forging and it is the most recently developed method of forging. This process takes place at a temperature above the work-hardening temperature of the workpiece, but below the temperature at which scale formation takes place. The lack of scale allows for the tolerances to be closer in the finished product.
Warm Forging Temperature Range
Depending on the physical properties of the individual workpiece, warm forging temperatures can range from 650 and 1000°C. Parts with simpler designs can be made at temperatures from 740 to 770°C, below the temperature at which a phase change occurs. However, parts made at these temperatures must undergo a heat treatment process after forging to ensure it maintains its new structure as it cools down.
Warm Forging Equipment & Material Considerations
Since warm forging temperatures are typically lower than those used in hot forging, the workpiece is less pliable during this process and complex shapes are harder to manufacture. Warm forgings also feature lower tolerances than cold forged parts. The most common metals that are used in warm forging are steel alloys. Warm forging makes it easier to deform steel alloys than in cold forging and can have better tolerances than those made with hot forging. These advantages contributed to the increased use of the warm forging manufacturing method, especially when creating high-volume automotive parts.
The equipment used in warm forging must be engineered to achieve an appropriate tooling life to increase cost-savings. This equipment should be compatible with the size and quality of the workpiece materials that will be forged using this method. Dies should be well maintained throughout their operational lives to increase lifetime.
Advantages | Disadvantages |
|
|
What is Hot Forging? (Application & Benefits)
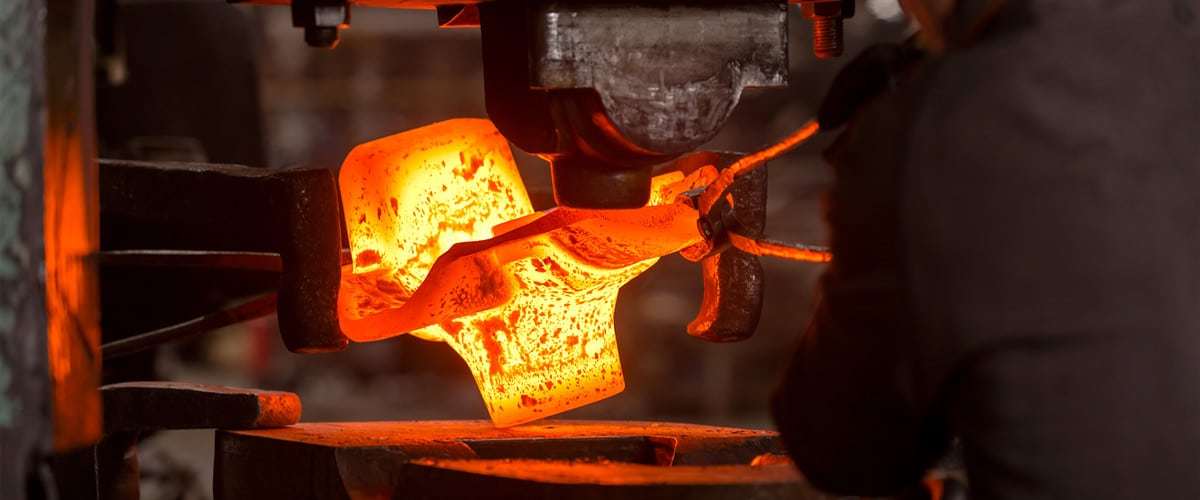
In forging terms, the metal object that must be deformed is commonly known as the billet or workpiece. The finished product is called the forging. In some forging methods, especially hot forging, the workpiece is placed inside a forge, a type of hearth that heats the metal to the desired working temperature before the shaping process can take place. Once the workpiece reaches the required temperature, tools, suh as forging hammers and forging presses, can be used to mold or deform the workpiece into a new shape or design.
Hot forging is the most well-known forging process. It operates above a given metal’s recrystallization temperature throughout the whole process in order to allow the forging to keep its newly-defined shape after it cools down. This high-temperature process changes the grain structure of the workpiece by breaking it down into finer grains. Heating a metal above its recrystallization or plastic deformation temperature prevents strain hardening of the material. Hot forging can manufacture complex metal designs that cooler forging processes cannot achieve at lower temperatures. This method not only changes the physical appearance of the starting metal, but also increases its ductility and toughness as a final product.
Hot Forging Temperature Range
Hot forging is typically conducted with metals that have a high formability ratio to prevent them from being damaged in the deformation process. Some of these metals include carbon steel, titanium, copper, aluminum alloys, and nickel alloys. There are some metals can only be hot forged due to their tough physical properties. The recrystallization temperature of steel can range from 400 to 700°C, but the hot forging temperature for steel can reach up to 1200°C. Due to the high temperatures at which this process takes place, the workpiece becomes more pliable and can be fashioned into intricate shapes. Once the forging is completely shaped, a strict cooling process ensues in order to set the forging in its new shape. Although rapid cooling is necessary in this process, cooling the material too quickly can also damage the finished piece. This cool down process must be handled very carefully in order to prevent the forging from warping.
Hot Forging Equipment & Material Considerations
The equipment needed for hot forging can vary by application of the finished product. Dies are metal blocks that are machined to contain forging impressions that are used to produce forgings. These dies are typically composed of a top and bottom die and are generally custom-made to match a customer’s desired shape to be used in the hot forging method. There are closed-die and open-die forms of forging. The open-die method uses dies that do not fully close around the workpiece, whereas the closed die method completely encases the workpiece. A forging press can also be used to place a large amount of pressure across an entire workpiece at once. Forging hammers apply force on localized areas of the workpiece.
Since the hot forging method is heavily temperature-dependent, the dies and other tools are preheated to limit a reduction in temperature of the workpiece during the process while it is in contact with the dies. This reduction in temperature is attributed to conductive heat transfer. The practice of heating equipment to the same temperature as the workpiece, led to the development of a specialized method of forging known as isothermal forging, a type of closed-die forging. Isothermal forging involves heating the metal and dies to the same temperature in a vacuum environment to avoid reductions in temperature due to conduction. The vacuum environment also limits any oxidation reactions that may occur between the metal workpiece and atmospheric gases. Another way to avoid oxidation is by covering the workpiece with a glass coating inside the furnace to prevent contamination or to feed an inert gas into the furnace. If oxidation of the workpiece takes place, it can lead to scale formation, damaging the finished product.
Advantages | Disadvantages |
|
|
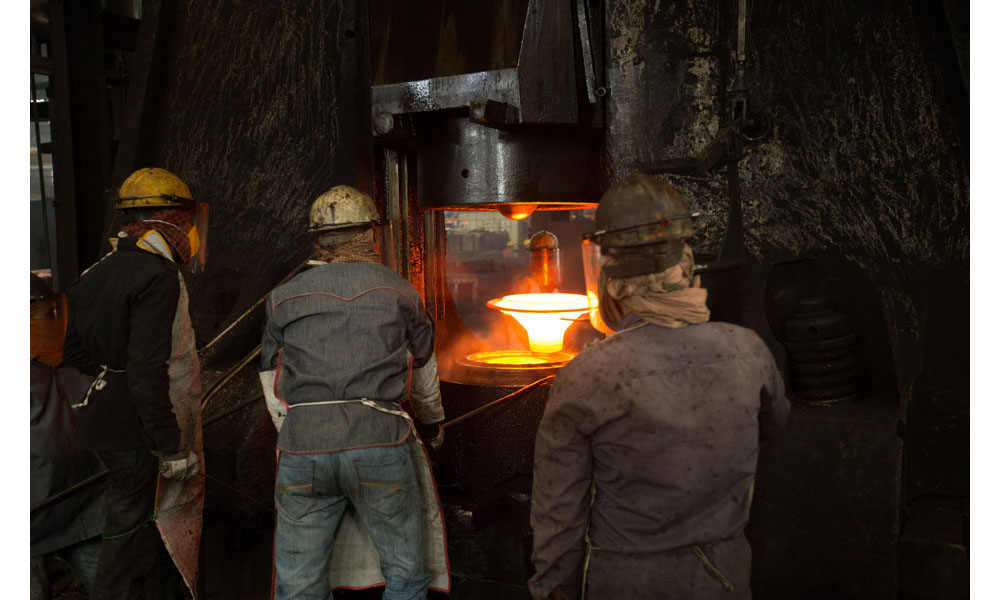