Warm Forging
Although hot forging has been around for centuries, the term warm forging originated sometime around 1950. Although they are different types of forging, they both involve shaping metal by compressive force. Forging parts at elevated temperatures reduces the tonnage necessary to deform the material. The necessity to decrease tonnage may be because of size, material hardness, or complexity of shape. Parts made by warm forging have better tolerances and surface finish than hot forgings, but not as good as cold forgings. Both processes offer a part with increased strength and durability but each method has distinct differences.
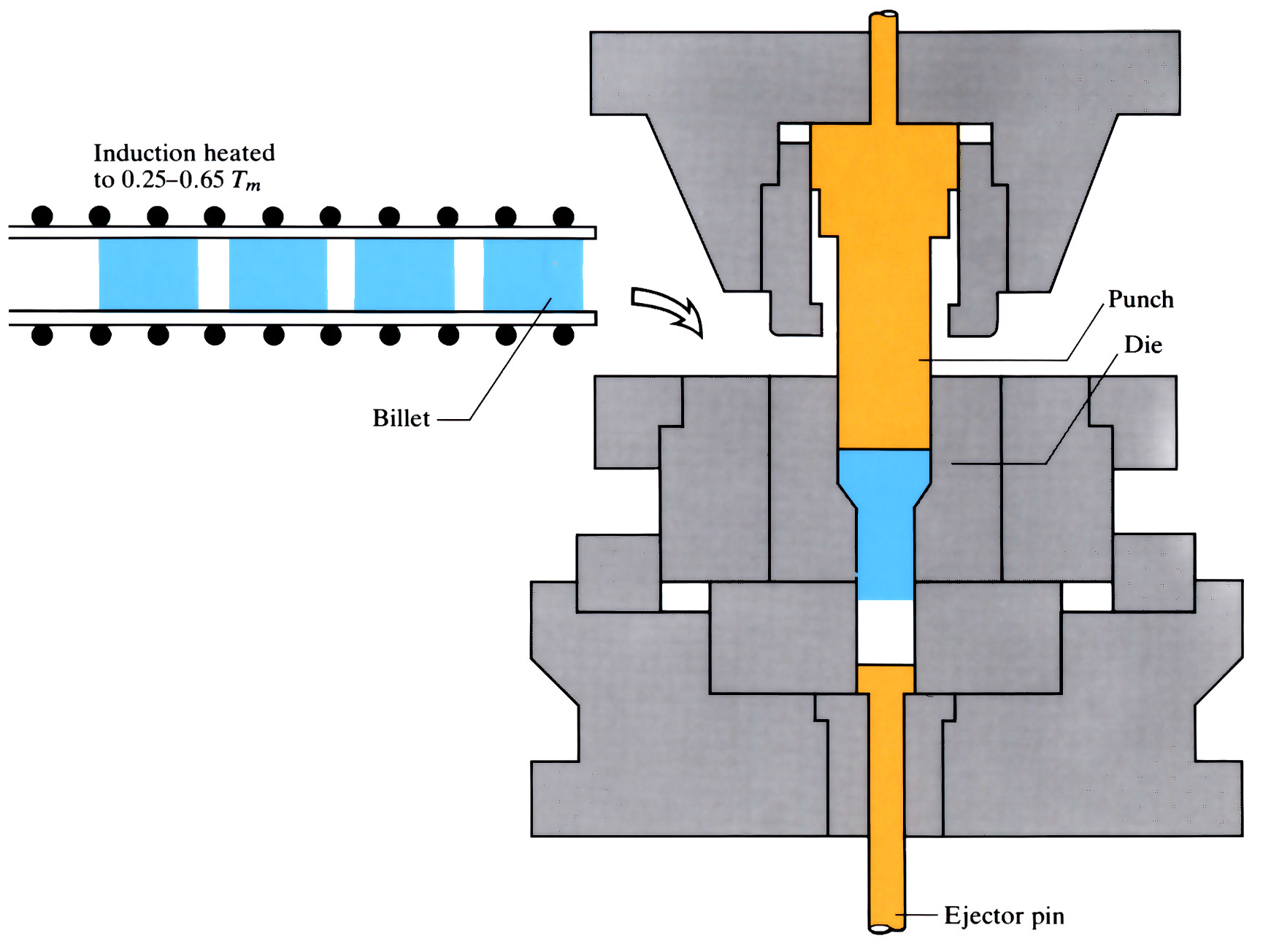
Warm Forging | Warm Extrusion
Although hot forging has been around for centuries, the term warm forging originated sometime around 1950. Although they are different types of forging, they both involve shaping metal by compressive force. Forging parts at elevated temperatures reduces the tonnage necessary to deform the material. The necessity to decrease tonnage may be because of size, material hardness, or complexity of shape. Parts made by warm forging have better tolerances and surface finish than hot forgings, but not as good as cold forgings. Both processes offer a part with increased strength and durability but each method has distinct differences.
Working metal above its re-crystallization temperature (1900-2300F) is called hot forging. Work hardening, also called strain hardening, in metal is caused by dislocation of the metallic crystal structure. Because hot forging takes place above the temperature at which the crystallization occurs, the grains deform to follow the shape of the parts but work hardening does not occur. Therefore, a greater amount of deformation is possible.
Warm forging occurs between room temperature and the re-crystallization temperature of the material (800-1800F). Although this allows work hardening to occur, the degree at which it happens is decreased. In addition, the materials yield strength is reduced and ductility increased, allowing for a greater amount of deformation to take place. Working the metal at a lower temperature than hot forging is beneficial to tooling life as well as part tolerances and surface finishes.
The workpiece billet is heated to temperatures between 0.25 and 0.6 Tm. A close fitting punch is used to exert pressure on the malleable metal billet held in a heated, closed die until forged to the required shape.
Warm forging of steel suction valve
- Requires accurate billet (±1 g).
- Billet does not need to be annealed unless combining cold and warm operations.
- Billet is heated by induction heater to 0.25–0.6 Tm (500–800°C for steel).
- Billet is lubricated with graphite (no need for phosphate/soap lubricants).
- Billet is warm forged in totally enclosed heated dies at lower loads than for cold forging.
Manufacture:
- Warm forging is used as an alternative process to cold forging, or is combined with cold forging.
- Usually applied for difficult-to-cold-forge materials such as alloy steels for induction hardening applications containing 0.4–0.5 wt% C.
- Requires accurate weight control of billets (±1 g).
- Billets are heated by induction heaters to temperatures of 0.25–0.6 Tm (e.g. steels are warm forged at 500–800˚C).
- The billets are then coated with graphite for lubrication during warm forging.
- These are then forged into totally enclosed dies with no flash formation.
- Hot work die steels are used for punches and dies.
- Lower forging loads are required than with cold forging, hence smaller-capacity presses can be used: e.g. maximum punch pressures for steel are:
cold forging (62% reduction) 2000 MPa
warm forging (62% at 600˚C) 1450 MPa - Any critical dimension might need to be tightened by the addition of an extra coining or sizing operation.
Materials:
- Generally the main advantage of warm forging over cold forging is that the range of materials can be extended from the soft metals into higher alloyed materials, which cannot normally be cold forged because of excessive forging loads on punches and dies.
- Low and medium alloy steels can be warm forged for higher duty applications or for applications requiring a change in post-heat treatment schedules (e.g. the change of low carbon case hardening steels to medium carbon (0.4–0.5% C) steels for induction hardening applications).
- Cr-Ni-V steels are used to produce socket heads for socket sets.
- Only a slight improvement in material properties compared with cold forging.
Design:
- Dimension and tolerance control is not as good as for cold forging.
- Tolerances:
diameter 0.3–0.6 mm
length 0.8–3.5 mm
flange thickness 0.3–0.5 mm - Surface finish: slightly oxidised on steel. 1.25–2.5 μm Ra.
The Advantages Of Warm Forging
Shaping metal by compressive forces is known as forging. Although there are different types of forging, they all offer a part with increased strength and durability. Its ability to save both time and material are just a few reason to consider forging as an alternative to other methods of manufacture.
The mechanical advantages of forging at higher temperatures include increasing the materials ductility and decreasing the metals yield strength. The ductility increase is due to the deformation taking place above the re-crystallization temperature. This increase in ductility results in an ability to form a more complex shape without the strain-hardening effects, resulting in fewer operations required to form the desired shape. In addition, the materials lower yield strength results in less force and therefore less energy required to forge the metal.
Although increase in forging temperature offers many benefits there are a few disadvantages to higher heat. One such disadvantage is surface finish. Although mostly due to the oxidation know as scale that occurs as the parts cool, there is also an increase in the erosion of the dies at high temperatures. This not only results in higher tooling costs, but also less precision due to the die wear and the shrinkage that occurs as the part cools.
Warm forging offers a happy median between cold forging and hot forging. Less energy is required for heating than hot forging, but less forging pressure is needed than cold forging. Less shrinkage and oxidation occurs resulting in greater precision than hot forging, and tooling costs are lower than cold forging. Overall, warm forging can provide a lower cost alternative with better quality for many of its applications.
Main Advantages of Warm Extrusion Over Cold Forging
Warm extrusion is one of the forging methods that stands between cold and hot forging. The technique does not work on billets at room temperature, not crystallization temperature. It simply requires the metal to be slightly heated.
When compared to cold forging, there many potential advantages that warm forging has over this forging process. These are the reasons why it is increasingly popular in the market. Below are some of the major benefits that come with warm forging when compared to cold forging.
Reduced Tooling Loads
One of the biggest benefits that come with warming forging billet is reducing the tooling loads. You will find out that cold forging requires a lot of tools to carry out the forging process. That will not be the case for warm forging because there is something in cold forging you will not need in warm forging. A good example of tools you won’t need are tools for heat treatment. This simply means a cheaper cost of investment.
Reduced Forging Press Loads
The other advantage that warm forging has over cold forging is the reduced forging press loads. The heating of the metal slug to temperatures slightly below crystallization makes it easier to forge the billet. The amount of pressing that would be needed for forging the metal was significantly reduced. Therefore, you will be spending less on the press equipment.
Increased Steel Ductility
The other advantage that comes with warm forging is the increased ductility of the forged steel. Ductility is one of the crucial elements of forged parts. You need to need forgings that offer good ductility to withstand the tress they are exposed to when working. A good example is mining bits, trenching teeth, or even grinder teeth. They are exposed to a lot of stress, and thus increased ductility will make them more effective.
Elimination Annealing
The other advantage of warm forging is the removal of the annealing step in the forging process. This is the heating process that is done to the cold forging parts to improve their mechanical properties. The annealing process enhances the mechanical properties of the forging parts. It means the forgings strong and harder, making it possible to withstand demanding conditions. The heating process is already covered for you.
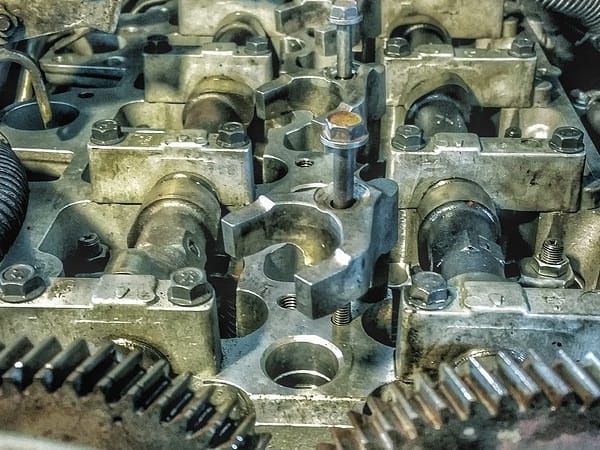