Press Forging
Press forging can be defined as the forming process of placing metal between two dies by applying mechanical or hydraulic pressure.Press forging is usually done on a forging press, a machine that exerts a gradual pressure on a forging die.The metal shape is usually formed by a single punch stroke for each die station.
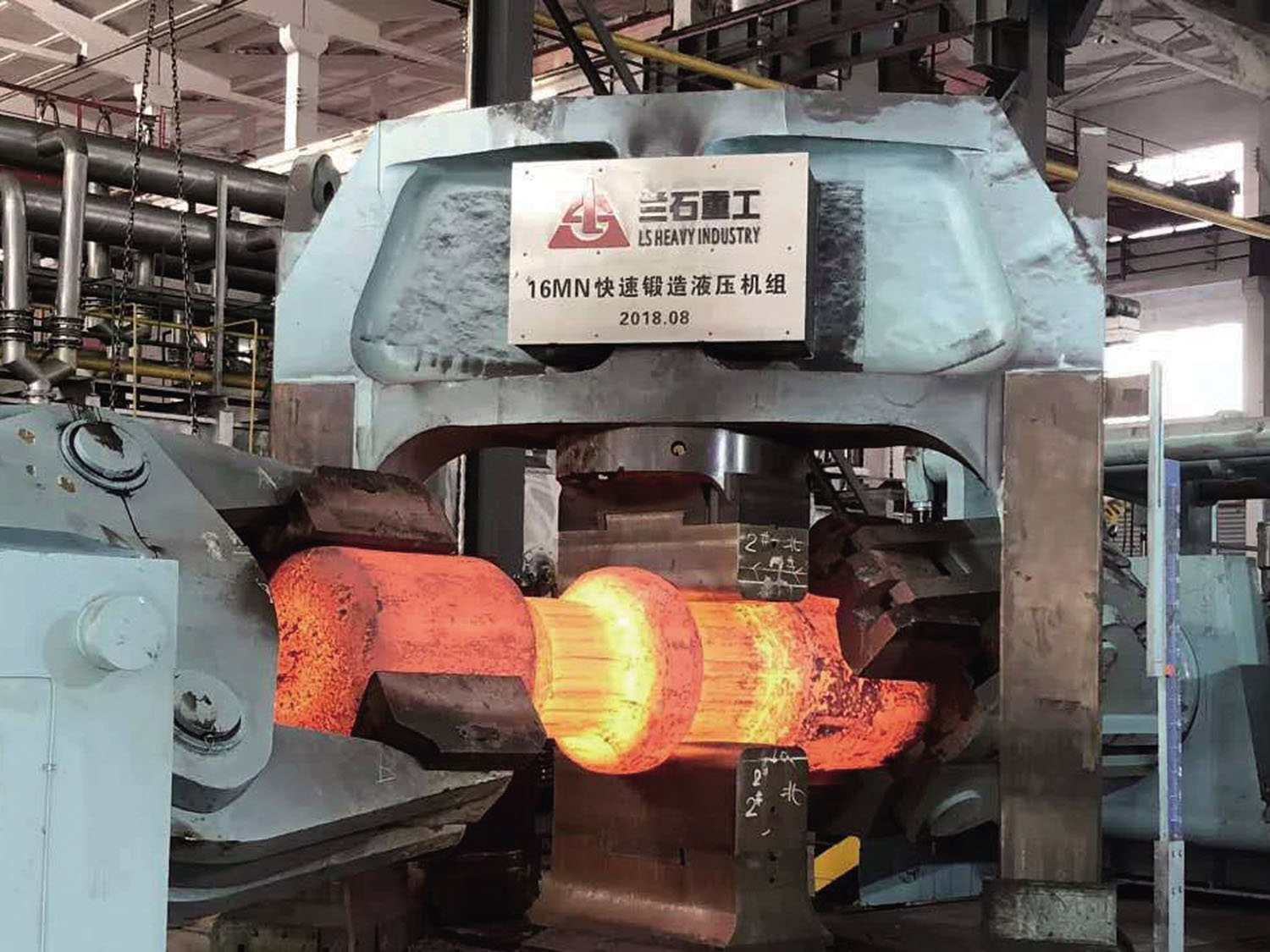
Press Forging
Press forging can be defined as the forming process of placing metal between two dies by applying mechanical or hydraulic pressure.Press forging is usually done on a forging press, a machine that exerts a gradual pressure on a forging die.The metal shape is usually formed by a single punch stroke for each die station.
Press forging can adopt hot forging or cold forging process. It is suitable for high volume productivity of forgings. The various forging operations in a press forge and its applications are described below.
Press forging is similar to drop forging except that it uses continuous extrusion pressure applied by a hydraulic press. This process increases the length of the workpiece and reduces the section of the workpiece.
.The key difference between impact forging and press forging is that in the former method a sudden impact force is applied on the die, while the latter exerts a gradually increasing pressure on the die.
Press forging process
Press forging is a process of applying progressive pressure to the die clamping the work piece.This can be done as an open die or closed die forging process.In an open die press forging process, the metal is surrounded only by one side of the die.For die pressing or closed die forging, the metal work piece is enclosed in a mold and pressure is applied to the mold.The work piece has plastic deformation and fills the mold cavity.
In both the processes, the forged part is pushed out of the die cavity by means of an ejector, as shown in Fig. 1:
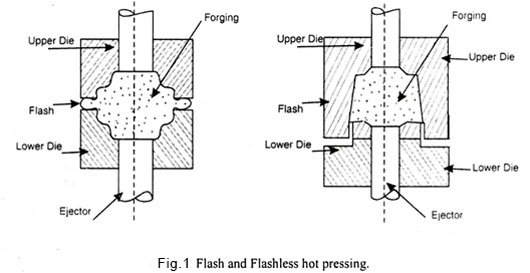
Both, hydraulic presses and mechanical presses are employed for press forging operation. The mechanical presses are used for light work while the hydraulic presses are employed for heavy work. Also, the mechanical press operates faster than the hydraulic presses but provides less squeezing force. Fig.2. Shows the sequence of operation, the estimated die life for production of bearing races.
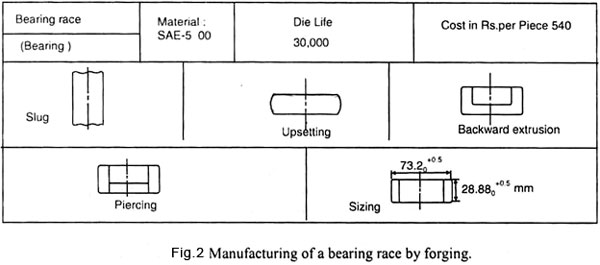
Press forging is a method of forging that involves the slow and continuous pressure on the workpiece. This method differs greatly from the heavy and quick blows used in drop and hammer forging. The contact of the workpiece in the die is measured in seconds whereas drop forging and hammer forging is measured in milliseconds. Press forging can be carried out either hot or cold.
Advantages of press forging:
- Higher productivity than drop forging.
- Greater accuracy in terms of tolerances within 0.01 to 0.02 inch.
- Dies used in press forging have less draft, therefore more complicated shapes can be forged with better dimensional accuracy.
- The speed, pressure and travel of the die are automatically controlled, in press forging.
- Possibility of process automation through mechanism of blank feeding and forging removal.
- The operation is completed in a single squeezing action, saves the time.
- The plastic deformation goes deep into the centre of the work piece, provides uniform and simultaneous deformation throughout the metal.
- The capacity of presses ranging from 500 to 9000 tons and the number of working strokes per minute can be high as 40 or even 50. Means 40 to 50 parts produced per minute.
- The press forging, therefore, is suitable for mass production of nuts, bolts, rivets, screws, break levers, bearing races, valves, etc.
Limitations of Press Forging:
Nevertheless, the press forging has certain limitations, these are:
- The initial capital cost is higher compared with drop forging, because the cost of crank press is always higher than that of an equivalent hammer.
- The difficulty of descaling the blank is another short coming of this process.
- The process is economically suitable only when the equipment is efficiently utilized.
Press forging may be defined as the process of shaping a metal that is placed between two dies by applying mechanical or hydraulic pressure. Press forging is usually done on a forge press - a machine that applies gradual pressure on the forging dies. The shape of the metal is usually accomplished by a single stroke of the press for each die station.
The key difference between impact forging and press forging is that in the former method a sudden impact force is applied on the die, while in the latter method a gradually increasing pressure is applied on the die.
Press forging may be undertaken as a hot or cold forging process. Press forging is suitable for high volume productivity of forgings. The various forging operations in a press forge and its applications are described below.
Technique of Press Forging
Press forging is a technique that applies gradual pressure on a die holding a work piece. This can be done as an open die or closed die forging process. In an open die press forging process, the metal is surrounded by the die on one side only. In the case of impression die or closed die forging methods, the metal work piece is enclosed in a die and pressure is applied on the die. Plastic deformation of the work piece occurs and it fills the die cavities.
Press forging in closed die method leads to less flash and needs less draft when compared to open die forging. Some of the common press forging methods that use closed dies are coining and hubbing.
Coining
This forging method is used to make coins. The metal is enclosed in a closed die and high pressures (almost 5-6 times the strength of the metal) are applied to obtain fine details of the die. Lubricants are not used in coining.
Hubbing
In this type of press forging, a pattern is pressed onto the die, such that the pattern flows into the die cavities. This process is often used in making of silverware.
Types of Forging Presses
The three main types of forging presses used for press forging are listed below:
- Mechanical Press – converts the rotation of the motor into linear motion of the ram.
- Hydraulic Press – hydraulic motion of the piston moves the ram.
- Screw press – screw mechanism actuates the ram movement.