Drop Forging
Although hot forging has been around for centuries, the term warm forging originated sometime around 1950. Although they are different types of forging, they both involve shaping metal by compressive force. Forging parts at elevated temperatures reduces the tonnage necessary to deform the material. The necessity to decrease tonnage may be because of size, material hardness, or complexity of shape. Parts made by warm forging have better tolerances and surface finish than hot forgings, but not as good as cold forgings. Both processes offer a part with increased strength and durability but each method has distinct differences.

Drop Forging | Drop Hammer Forging
Drop forging is a type of closed-die forging. It is used when a large quantity of certain components with sound and good quality forgings are to be produced.
The typical products obtained in drop forging are connecting rod, crank, crank shaft, crane hook, etc. Drop forging process is widely used in automobile industries, airplane parts manufacturing, rail road equipment manufacturing, engine manufacturing industries, agricultural equipment manufacturing industries, etc.

In drop forging one material is put into the die and hammering action continues on the die anvil until it takes desired shape. Wrenches, piston and crankshaft are typical example of automobile parts made under forging operation.
Drop forging is a type of closed-die forging. It is used when a large quantity of certain components with sound and good quality forgings are to be produced.
Drop Forging Process
Step 1. Dies design & making
Making dies is the first step for starting drop forging process. We will first design and produce dies according to the die drawing. Such dies normally include forging dies, trimming dies and flat die. Among these dies, flat die is not necessary, as it is just used to flatten the products to ensure geometric tolerances.
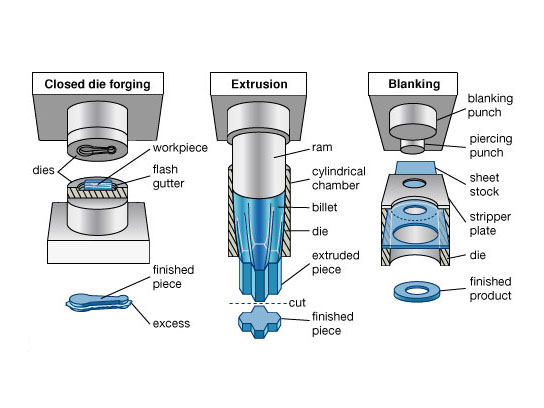
Step 2. Billet cutting & heating
Normally, we will prepare commonly used materials (steel, aluminum & copper) in stock, and cutting the billet to the estimated size. Then using the medium frequency furnace to heat the billets to a certain temperature, after that deliver the heated bars to a metal frame and wait for forging.
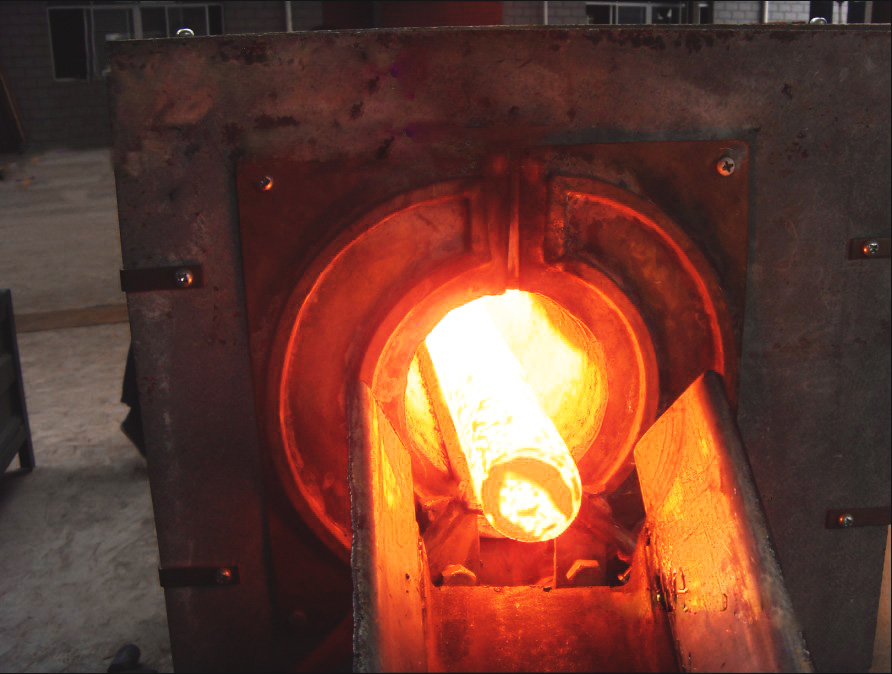
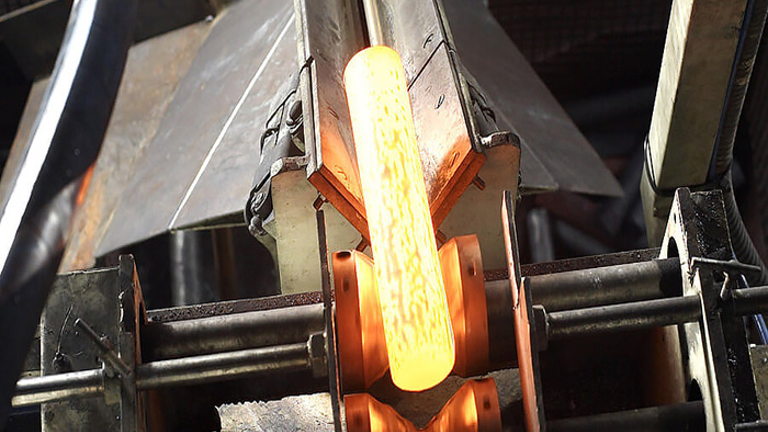
Step 3. Drop forging
Before forging, forging upper and lower dies will be attached to the anvil of forging press. Then workers will pick up a billet and place between forging dies so that the billet will be pressed at a high speed for several times to desired shapes.
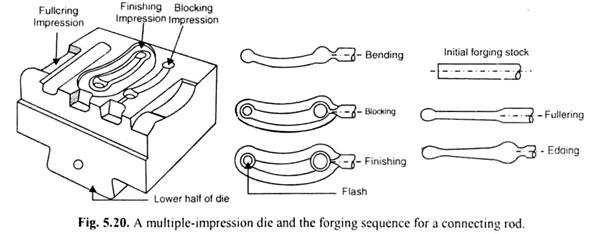
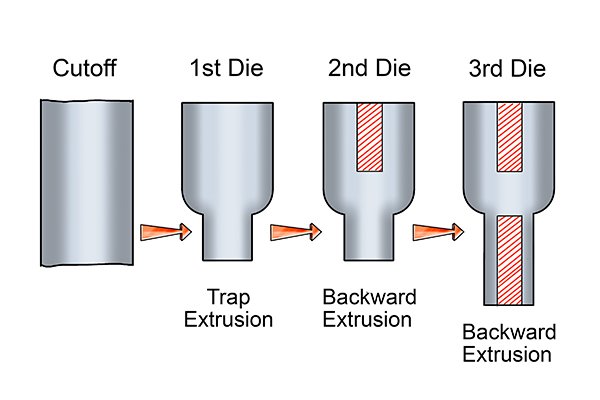
Step 4.Trimming
After forging, we will see the redundant flash around the drop forging blanks. So, removing flash is also a necessary step. Workers will first assemble the trimming dies under the punching machine, and then press the forging blanks at a time so that flash will be removed. We call this process "trimming".
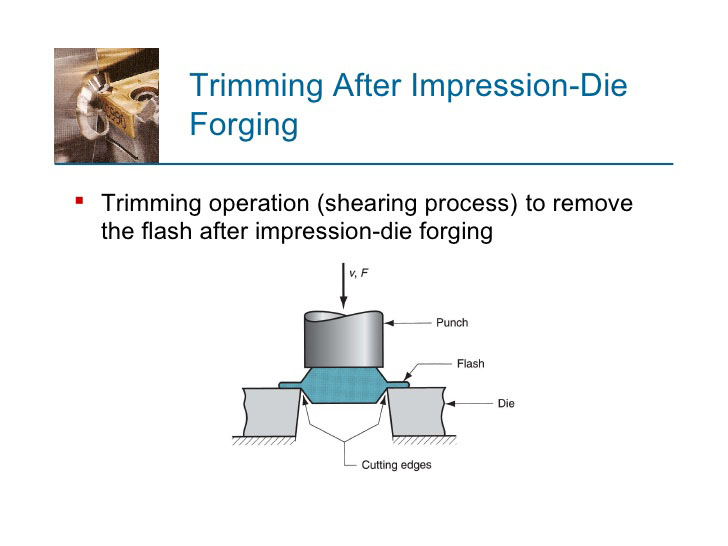
Step 5. Heat treatment
Heat treatment will help to reach the required mechanical properties and hardness. Such heat treatment processes are normalization, quenching, annealing, tempering and hardening, solution treatment, etc.
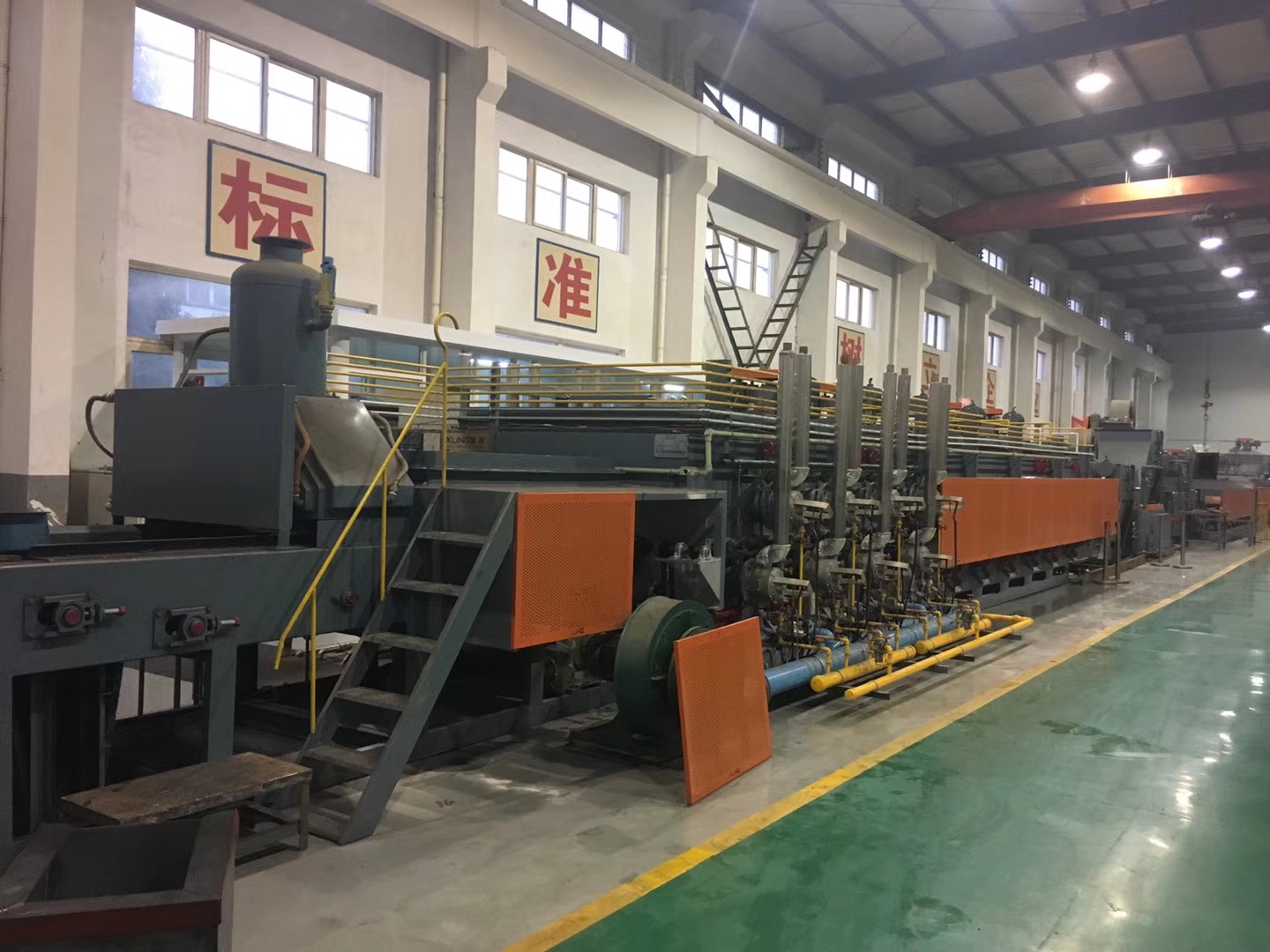
Step 6. Shot blasting
By shot blasting, the drop forgings will look more smooth and clear. You will see a better surface finish. Normally, the surface finish of drop forging products will reach Ra6.3, whose surface is much better than that of lost wax casting.
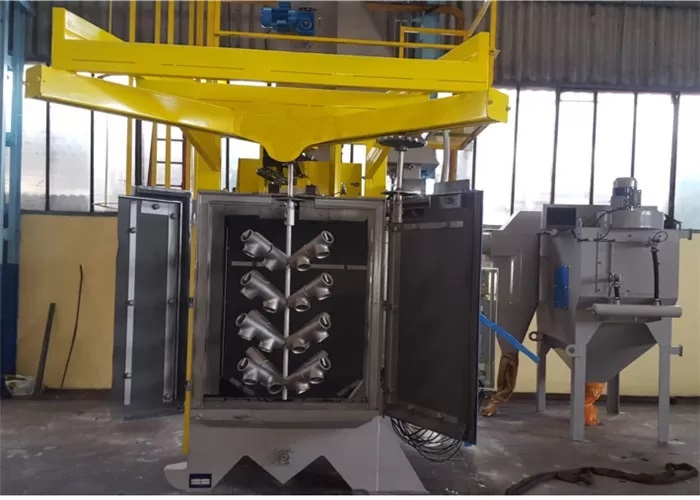
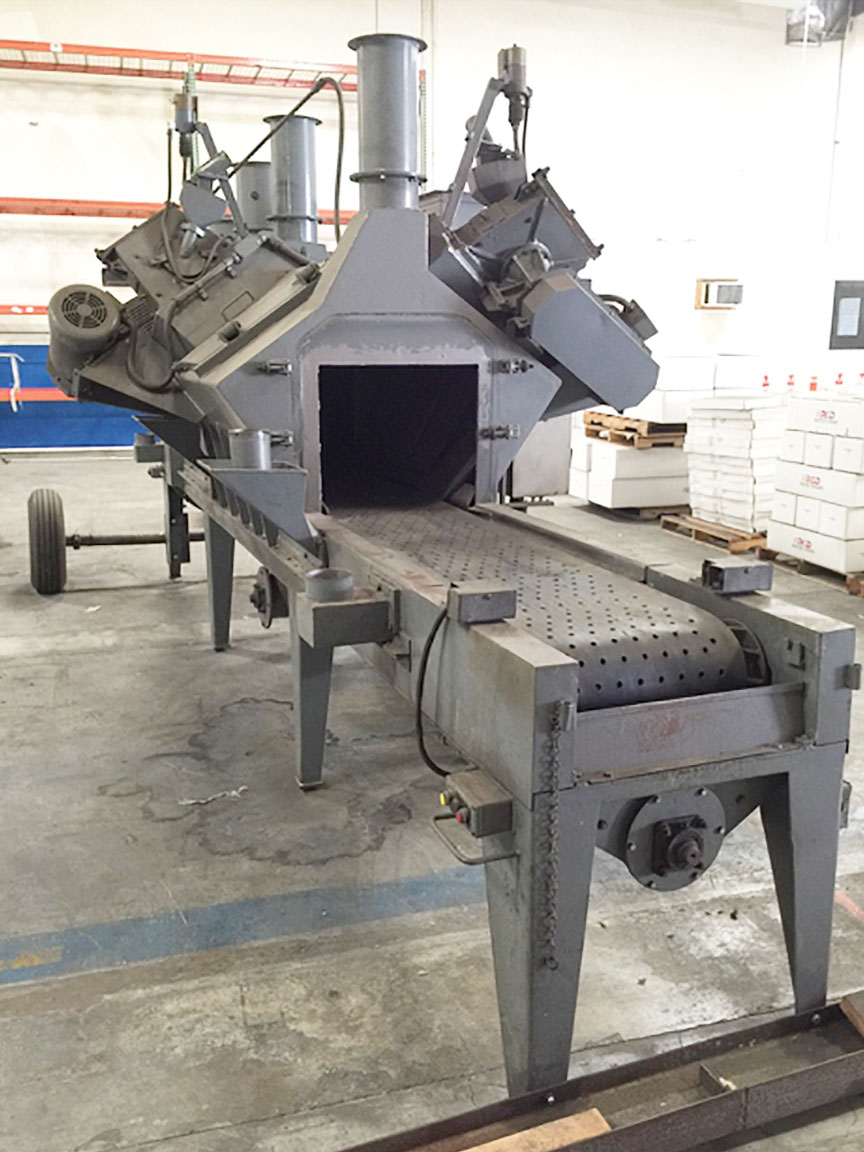
Step 7. Machining
For some parts, drop forging process is not enough to get the required tolerance, then machining will be workable, we will do machining with different machining facilities, such as milling machine, boring machine, drilling machine, grinding machine, CNC, etc.

Step 8. Surface treatment
In most cases, we will just do water/oil anti-rust on the surface of drop forgings if there is no special requirement. But we could also follow other surface treatment demands, like painting, powder coating, galvanization, electro painting, etc. according to the requirement of our customers.
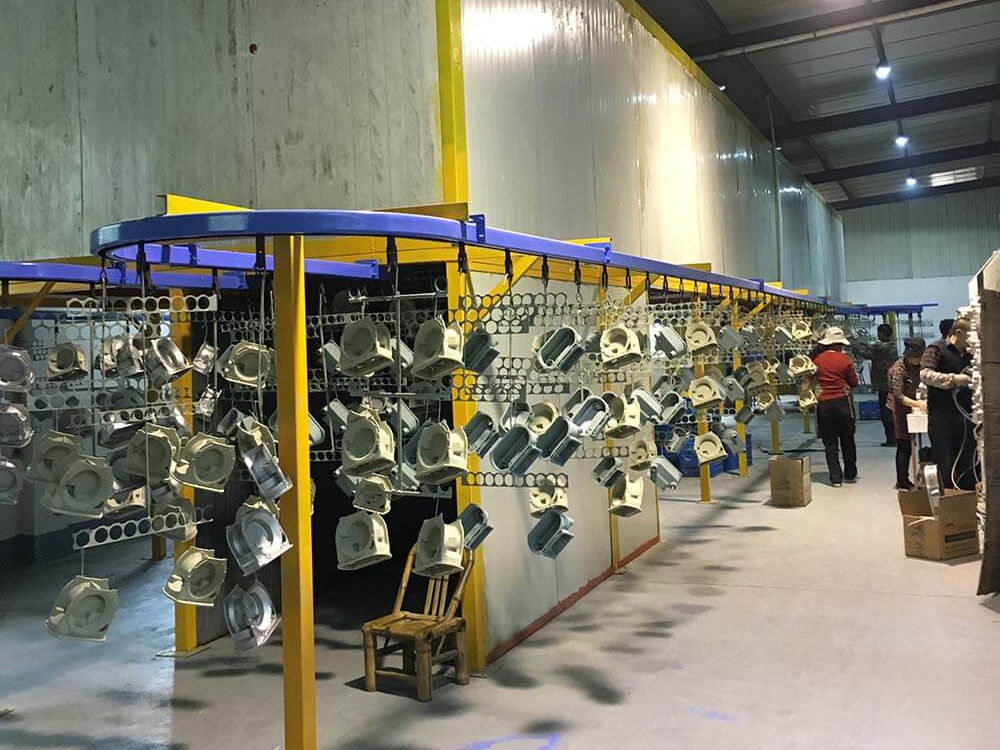
Step 9. Final inspection
To ensure superior quality, we must do dimension inspection. Sometimes, we also need to do inspection for mechanical properties and chemical composition.
Step 10. Package & Delivery
Usually, we will pack the forgings with polybag, and put in a strong wooden case. Such package could also be customized to meet customer's demand. Located in Zhangjiagang, both Shanghai seaport and airport are very convenient for us to deliver products to our customers' destination port.

Advantages of Drop Forging:
1. Good grain flow is achieved.
2. Faster speed of operation.
3. Good strength of material is obtained.
4. Little or no wastage of material.
Disadvantages of Drop Forging:
1. Die preparation is a costly process.
2. Die impression requires a good skill of work.
3. Die maintenance is costly.
4. Part requires little lifting between successive blow to avoid heating of die.
5. Flash produced must be trimming off to get final shape.
What Is Drop Hammer Forging?
The manufacturing industry plays a major role in the national economy. It also literally creates as well as maintains modern lifestyles through the components it produces. These items are not just end products, such as clothing or athletic shoes you shop for at the mall. This industry also makes specialized tools that make fabricating end products possible. Manufacturers have developed various methods to make particular items. One of these processes is called drop hammer forging. The drop forging process ultimately helps make your life more comfortable and convenient.
Technique Basics
What is drop hammer forging? Simply put, it is a fabrication method employing two dies, one on a stationary anvil and the other attached to a moving ram.
- Heated metal is placed onto the lower die.
- The ram brings the other die down, delivering a set number of blows to shape the hot metal.
- The number of blows needed varies depending upon the item being manufactured.
The drop forging process is aptly named, and while it sounds simple, a great deal of power is involved. In some cases, the upper hammer on the ram may be dropped using the force of gravity alone. However, it is also common for mechanical force to be applied to move the hammer. Some hammers can drop with a pressure of 50,000 pounds. At CHISEN® Forging, we use this technique to produce components for numerous industries, including the aerospace, automotive, agricultural, and material handling sectors.
Advantages of Drop Hammer Forging
Now that you know what drop hammer forging is, here are some of the advantages this focused manufacturing process offers:
- No wasted material
- Strong parts with good mechanical properties
- Fast production method
The drop hammer process also makes it possible to align metal grains along with potential stress locations, which improves overall strength. The components we make using this process are generally stronger and work for longer in high-stress conditions, making this process a valuable operational aspect of the manufacturing industry.
Drop Hammer Products
Drop hammer forging is an efficient way to produce specialty components and tools. Examples include:
- Gears
- Levers
- Connecting rods
- Crankshafts
- Spanners
This manufacturing process allows us to fabricate items based on specific requirements and needs. Just as the lone blacksmith formerly used his strength to swing hammers to produce metal objects such as horse shoes and wheels, we also apply force to shape metal. Our techniques, though, allow for broader scope because we employ advanced machine hydraulics along with human skill in our high-precision drop hammer process.
Considerations With This Production Method
While the drop hammer process offers many advantages, it requires an advanced manufacturing process itself. The die must be created, which can be expensive. Skilled metal workers must use special equipment to make accurate die. These specialized parts must then be maintained so that they keep their original integrity. This process is also time-consuming and costly.
Also, if the finished parts have excess metal on them, which is called flash or flashing, it must be trimmed off to achieve the final form. This also takes time and money. Overall, though, drop hammer forging is worth the time and work put into it because it produces accurate components that meet the exacting requirements of today’s high-tech manufacturing sectors.
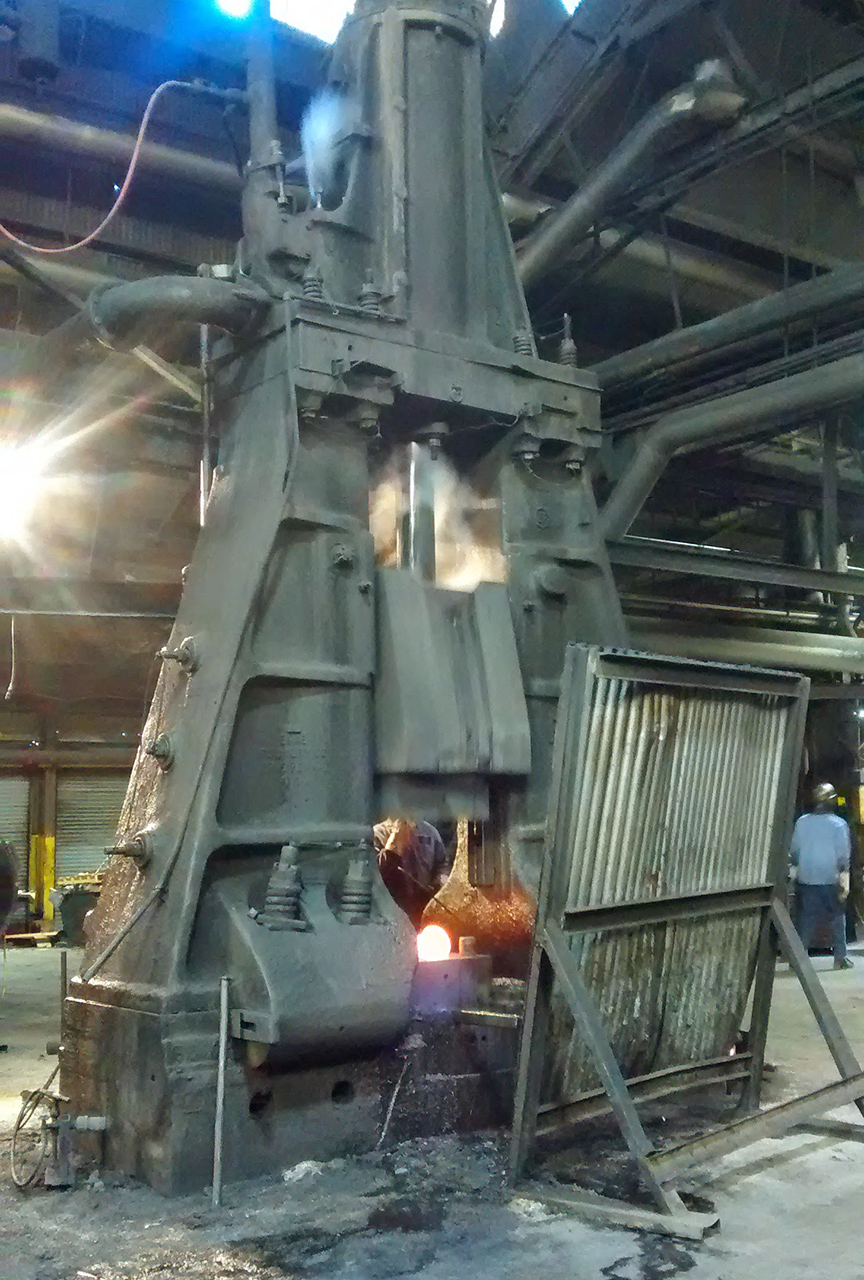