AISI 1040 Carbon Steel (UNS G10400)
AISI 1040 carbon steel has high carbon content and can be hardened by heat treatment followed by quenching and tempering to achieve 150 to 250 ksi tensile strength.
AISI 1040 Carbon Steel (UNS G10400)
Introduction
AISI 1040 carbon steel has high carbon content and can be hardened by heat treatment followed by quenching and tempering to achieve 150 to 250 ksi tensile strength.
The following datasheet gives an overview of AISI 1040 carbon steel.
Chemical Composition
The following table shows the chemical composition of AISI 1040 carbon steel.
Element | Content (%) |
---|---|
Iron, Fe | 98.6-99 |
Manganese, Mn | 0.60-0.90 |
Carbon, C | 0.370-0.440 |
Sulfur, S | ≤ 0.050 |
Phosphorous, P | ≤ 0.040 |
Physical Properties
The physical properties of AISI 1040 carbon steel are tabulated below.
Properties | Metric | Imperial |
---|---|---|
Density (chemical composition of 0.435% C, 0.69% Mn, 0.20% Si, annealed at 860°C (1580°F)) | 7.845 g/cc | 0.2834 lb/in³ |
Melting point | 1521°C | 2770°C |
Mechanical Properties
The mechanical properties of AISI 1040 carbon steel are outlined in the following table.
Properties | Metric | Imperial |
---|---|---|
Tensile strength | 620 MPa | 89900 psi |
Yield strength | 415 MPa | 60200 psi |
Bulk modulus (typical for steels) | 140 GPa | 20300 ksi |
Shear modulus (typical for steels) | 80 GPa | 11600 ksi |
Elastic modulus | 190-210 GPa | 27557-30458 ksi |
Poisson’s ratio | 0.27-0.30 | 0.27-0.30 |
Elongation at break (in 50 mm) | 25% | 25% |
Reduction of area | 50% | 50% |
Hardness, Brinell | 201 | 201 |
Hardness, Knoop (converted from Brinell hardness) | 223 | 223 |
Hardness, Rockwell B (converted from Brinell hardness) | 93 | 93 |
Hardness, Rockwell C (converted from Brinell hardness. Value below normal HRC range, for comparison purposes only) | 13 | 13 |
Hardness, Vickers (converted from Brinell hardness) | 211 | 211 |
Izod impact (annealed at 790°C (1450°F)) | 45 J | 33.2 ft-lb |
Izod impact (as rolled) | 49 J | 36.1 ft-lb |
Izod impact (normalized at 900°C (1650°F) | 65 J | 47.9 ft-lb |
Thermal Properties
The thermal properties of AISI 1040 carbon steel are given in the following table.
Properties | Metric | Imperial |
---|---|---|
Thermal expansion co-efficient (@ 20-100°C/68-212°F, composition of 0.40% C, 0.11% Mn, 0.01% P, 0.03% S, 0.03% Si, 0.03% Cu) | 11.3 µm/m°C | 6.28 µin/in°F |
Thermal conductivity (@ 100°C/212°F) | 50.7 W/mK | 352 BTU in/hr.ft².°F |
Thermal conductivity (@ 0°C) | 51.9 W/mK | 360 BTU in/hr.ft².°F |
Other Designations
Other designations that are equivalent to AISI 1040 carbon steel include:
- ASTM A29 (1040)
- ASTM A510 (1040)
- ASTM A513
- ASTM A519 (1040)
- ASTM A546 (1040)
- ASTM A576 (1040)
- ASTM A682 (1040)
- ASTM A827
- ASTM A830
- MIL S-11310 (CS 1040)
- MIL S-16788
- MIL S-46070
- SAE J1397 (1040)
- SAE J403 (1040)
- SAE J412 (1040)
Fabrication and Heat Treatment
Machinability
The machinability rating of AISI 1040 carbon steel is 60.
Forming
AISI 1040 carbon steel can be formed in the annealed condition.
Welding
AISI 1040 carbon steel can be welded using all welding techniques. It can be pre-heated at 149 to 260°C (300 to 500°F) and post-heated at 594 to 649°C (1100 to 1200°F) due to its high carbon content.
Heat Treatment
AISI 1040 carbon steel can be heat treated at 844 to 899°C (1550 to 1650°F) followed by quenching in water and tempering.
Forging
AISI 1040 carbon steel can be forged at 982 to 1260°C (1800 to 2300°F).
Hot Working
AISI 1040 carbon steel can be hot worked from 94 to 483°C (200 to 900°F ).
Cold Working
AISI 1040 carbon steel can be cold worked in the annealed state using conventional methods.
Annealing
AISI 1040 carbon steel can be annealed at temperatures ranging from 872 to 983°C (1600 to 1800°F). It can be then slowly cooled in the furnace. Stress relief annealing process can be performed at a temperature of about 594°C (1100°F). Normalizing treatment can also be performed at 899°C (1650°F) followed by cooling slowly.
Tempering
AISI 1040 carbon steel can be tempered at 316 to 705°C (600 to 1300°F) based on the desired strength.
Hardening
AISI 1040 carbon steel can be hardened by performing cold working process.
Applications
AISI 1040 carbon steel can be used in couplings, crankshafts, and cold headed parts
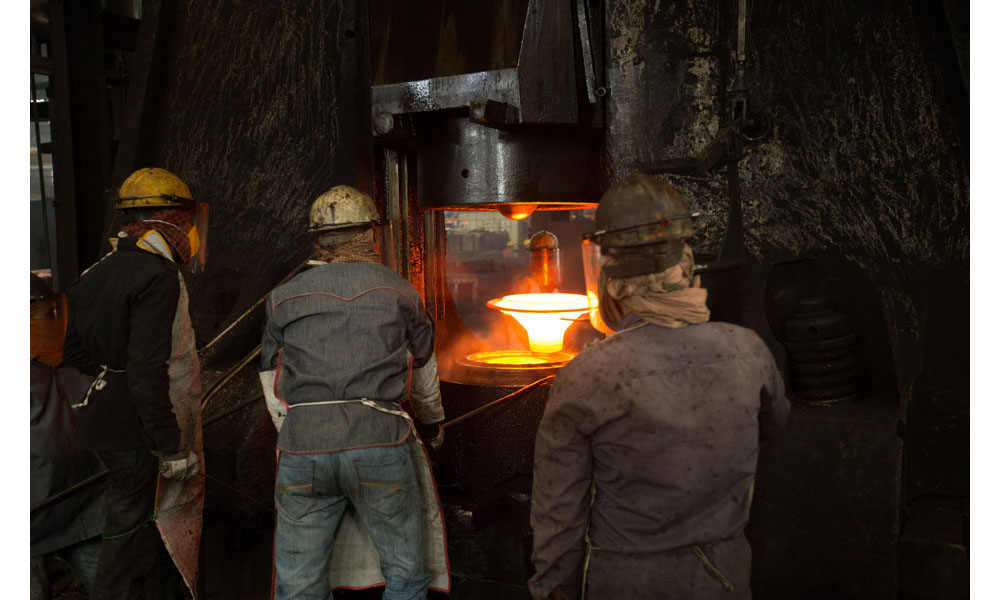